Panel Rockwool The Ultimate Solution for Insulation Needs
Rockwool panel is one of the best insulation panels available today. Are you looking for a reliable and efficient solution to insulate your building? Look no further! Panel rockwool, also known as sandwich rockwool, is the answer to your insulation needs. With its exceptional thermal and acoustic properties, panel rockwool offers superior performance and durability. In this comprehensive guide, we will explore everything you need to know about panel rockwool, including its benefits, applications, pricing, manufacturing process, and weight considerations. So, let’s dive in and discover why panel rockwool is the ultimate choice for insulation.
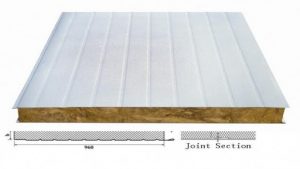
What is Panel Rockwool?
Panel rockwool, often referred to as sandwich rockwool, is a type of insulation material made from volcanic rock or basalt. It is manufactured by melting the rock at extremely high temperatures and then spinning it into thin fibers. These fibers are then compressed and bonded together to form rigid panels, creating a highly effective insulation material.
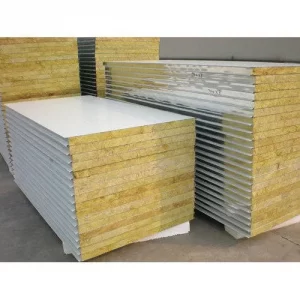
Benefits of Panel Rockwool
- Outstanding Thermal Insulation: Panel rockwool has exceptional thermal insulation properties, making it an ideal choice for both residential and commercial buildings. It effectively reduces heat transfer, keeping the interior spaces cool in summer and warm in winter.
- Superior Acoustic Insulation: One of the standout features of panel rockwool is its excellent sound absorption capabilities. It efficiently absorbs and dampens noise, making it perfect for environments where noise reduction is crucial, such as recording studios, theaters, and office spaces.
- Fire Resistance: Panel rockwool is non-combustible and offers outstanding fire resistance. It does not contribute to the spread of flames, providing valuable time for occupants to evacuate during a fire incident.
- Energy Efficiency: By minimizing heat loss or gain through walls, roofs, and floors, panel rockwool significantly improves the energy efficiency of buildings. This, in turn, leads to reduced energy consumption and lower utility bills.
- Durability and Longevity: Panel rockwool is highly durable and has a long lifespan. It does not sag or deform over time, ensuring its performance remains intact for years to come.
Applications of Panel Rockwool
Panel rockwool’s versatility allows it to be used in various applications across different industries. Let’s explore some of the common uses of panel rockwool below:
1. Building Construction and Renovation
Panel rockwool is extensively used in both new construction projects and renovation works. It is employed in wall systems, roofs, facades, and partition walls to provide excellent thermal and acoustic insulation. Its lightweight nature makes it easy to handle and install.
2. Industrial Insulation
In industrial settings where temperature control is critical, panel rockwool acts as an insulating barrier. It is widely used in factories, warehouses, power plants, and refrigeration units to maintain stable internal temperatures and prevent energy losses.
3. HVAC Duct Insulation
The efficient thermal and acoustic properties of panel rockwool make it suitable for insulating HVAC (heating, ventilation, and air conditioning) ducts. By minimizing heat loss or gain in the ductwork, it helps maintain desired temperatures and reduces energy consumption.
4. Soundproofing Solutions
Due to its exceptional sound absorption capabilities, panel rockwool finds extensive use in soundproofing applications. Whether it’s recording studios, cinemas, or conference rooms, using panel rockwool significantly enhances the acoustic quality of these spaces.
Understanding Panel Rockwool Price Factors
When considering panel rockwool for your insulation needs, understanding the price factors is crucial. Several elements impact the cost of panel rockwool, including:
- Thickness and Density: Thicker and denser panel rockwool tends to have a higher price due to the increased material usage and improved insulation properties.
- Size and Coverage Area: The dimensions and coverage area of the panel rockwool panels affect the overall cost. Larger panels or customized sizes may incur additional expenses.
- Supplier and Manufacturer: Different suppliers and manufacturers may offer varying prices for panel rockwool. It is advisable to research and compare prices from reputable sources to ensure competitive pricing without compromising quality.
Manufacturing Process of Panel Rockwool
The production of panel rockwool involves several stages. Let’s take a closer look at the manufacturing process:
- Raw Material Preparation: Basalt rocks are crushed and mixed with recycled rockwool waste to create a homogeneous blend.
- Melting and Fiberizing: The blended material is then melted at high temperatures (around 1500°C) in a furnace. The molten material is spun into fibers using a spinning wheel, creating a wool-like consistency.
- Bonding and Curing: The loose rockwool fibers are collected and compressed between two facings, such as metalsheets or fiberglass mats. The panels are then cured in an oven to solidify the bonding agents and ensure structural integrity.
- Cutting and Shaping: Once cured, the panel rockwool is cut into desired sizes and shapes using specialized cutting machinery. This allows for customization based on specific project requirements.
- Quality Control and Packaging: The final step involves rigorous quality control inspections to ensure that the panel rockwool meets industry standards. The panels are then packaged and prepared for distribution to suppliers and end-users.
Considerations for Panel Rockwool Weight
The weight of panel rockwool is an essential factor to consider during installation. Here are a few key points to keep in mind:
- Structural Load Capacity: Before installing panel rockwool, it is crucial to assess the structural load capacity of the building. Ensure that the load-bearing elements can support the weight of the insulation panels without compromising the integrity of the structure.
- Handling and Installation: Lightweight panel rockwool is easier to handle and install, reducing the risk of strains or injuries during the installation process. It is advisable to consult installation guidelines provided by manufacturers for proper handling techniques.
- Impact on Transportation: If you are transporting panel rockwool over long distances, the weight can affect shipping costs and logistics. Opting for lightweight options may help minimize transportation expenses.
In conclusion, Rockwool panel is an exceptional insulation material with numerous benefits, including thermal and acoustic insulation, fire resistance, energy efficiency, durability, and longevity. Its applications span across various industries, making it a versatile choice for both new construction projects and renovation works. Understanding price factors, the manufacturing process, and weight considerations will assist you in making informed decisions when selecting panel rockwool for your insulation needs. So why compromise? Choose panel rockwool and experience the ultimate solution for insulation!
Read more here